A perspective to give the job description »printer« new attractiveness – Dieter Finna · pack-consult.com (Click here for a German version)
Since the spring of 2022, just as the industry was beginning to recover from the economic and social effects of the pandemic, HR managers in numerous industries have been asking themselves: Where are our employees, where are our young people? This situation revealed a labour shortage that began well before the pandemic. The reasons for this are obvious. But what to do to change this?
You don’t have to look far to understand the reasons for the younger generation’s disinterest in the printing industry. The fact that it is not very attractive to young people when choosing a career is mainly due to a perceived image. Numerous company closures in the commercial sector as well as the environmental problems of packaging have shaped the image of the industry. In an overall competitive labour market, it is currently not very attractive.

Yet label and packaging printing has a lot to offer. According to one study*, bottlenecks in skilled workers are mainly to be found in gender-typical professions, i.e., professions that are mainly practiced either by women or by men. Such hindrances are not as likely to exist in occupations that are equally attractive to women and men. For the printing industry, this means emphasizing the attractive employment prospects in label and packaging printing for women and men alike, as well as their crisis-proof and future-proof jobs.
After all, packaging printing is an industry in which fundamental parameters are currently being rethought. A market where the shift towards more environmentally friendly, sustainable materials and print designs is in full swing. An industry that is dominated by media technology and where presses are increasingly controlled via an HMI (Human Machine Interface) like a smartphone. These developments help make it interesting for female and male trainees alike.
Mechanical engineering drives automation forward
What the industry has learned is that there is a growing shortage of operators for machines where there is little or no automation. The pandemic has also shown that if skilled workers are absent, printing presses can no longer be operated. This is one of the reasons that mechanical engineering companies like Gallus Ferd. Rüesch AG are breaking new ground. Their developments support the converter’s efforts to counter the shortage of skilled workers through automation.
The Swiss mechanical engineering company, whose name stands for conventional and hybrid narrow web technology in the market, recently surprised the industry with the presentation of the Gallus One. With this model, the company is bringing an independent digital printing machine into the market and is thus pursuing the clear goal of preparing the digital transformation in narrow web printing for upcoming requirements. Pure digital printing is a practical option to renew the machine park, since high-end hybrid machines are out of the question for many converters due to their capital requirements.
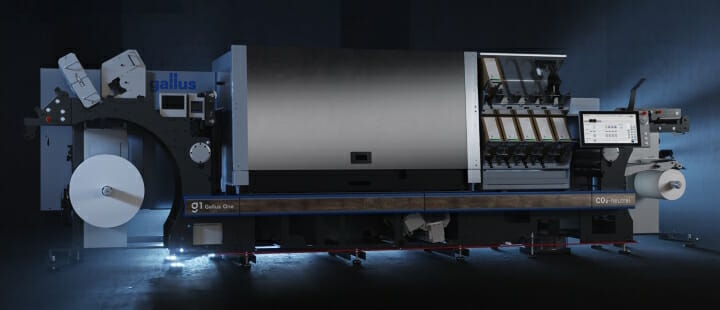
Digital printing is changing the job description »printer«
What is exceptional about the Gallus One machine concept is the extensive standardization which has been incorporated into the digital machine. It’s defined process parameters are designed for consistent automation, which enables the operator to confidently complete the demanding tasks in day-to-day business.
The high level of automation of the Gallus One changes the field of activity at the press. Self-monitoring of basic functions on the digital press frees the operator from time-consuming routine tasks. No more manual make-ready as in conventional printing, no more manual mixing of inks, no more colour changes, no more adjusting of inks and many other manual activities. These are eliminated in digital printing.
Here, the operator carries out the order change with predominantly IT-related activities. They take the print data from the pre-press stage with integrated colour management and load it into the frontend that controls the digital printing machine. They then selects the appropriate substrate profile for printing. This processed data is then printed with high production reliability and productivity. The orders are completed with a data backup. Apart from material handling, process steps that are carried out via the control console characterize and automate the job description of the machine operator in digital printing.
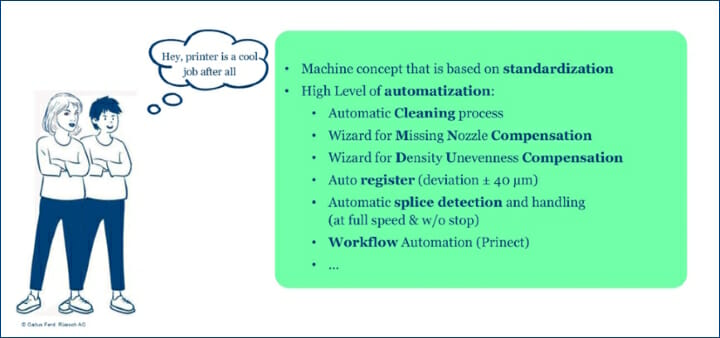
Gallus One with additional ease of use
What makes the Gallus One technology a particularly attractive workplace for young professionals? Thanks to its extensive level of automation, the machine offers a level of operating convenience that is well above the standard. An operator controlling the machine via the human-machine interface (HMI) receives all important information from it directly on the display.
During operation a proprietary image processing system (Vision System) takes over several functions serving as the heart of the central machine, and is the basis for the high level of automation. One of these time-saving functions is the user-friendly adjustment of register settings at the push of a button. This ensures that the individual colours are precisely superimposed. The Vision System with its high-resolution camera outperforms comparable solutions by automating essential quality assurance measures detecting not only missing nozzles, but also density variations (Density Uneveness) in solids. Compensating for these two sources of error prevents both white lines in the print image and the formation of rainbow effects that would cause colour drift in solids.
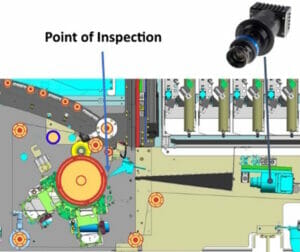
The Gallus One has other user-friendly functions that make working on the machine a pleasure. With the Gallus One, the print heads are not moved – not even for cleaning. This innovative concept minimizes service calls and increases machine availability. The newly designed cleaning system moves the entire substrate table down in the printing area, giving access to the print heads as a whole – including web tension control. When cleaning is triggered by the operator, the cleaning unit is then brought to the print heads and cleans them. In addition to this standard cleaning through the use of the innovative features of the cleaning system, ultrasonic cleaning can be activated to support the cleaning process as needed. This makes the entire process extremely simple for the operator, with the aim of replacing manual cleaning as completely as possible.
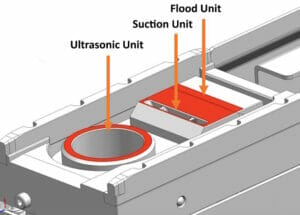
The glass covers of the pinning modules, which fix the ink droplets directly after they hit the substrate using UV light, are just as easy to clean. Their cleaning takes place outside the press, without any contortions during the cleaning process. Both of these solutions make working on and with the press easier.
Refilling ink is also very user-friendly. For improved ink handling, the ink containers are easily accessible from the operator side. This design allows the containers to be changed without the operator coming into contact with ink, while the machine continues to run, so there is no need to schedule downtime or need to correct the web.
Additionally, the operator does not have to worry about splices in the parent roll. The Gallus One has an automatic detection system that works via sensors detecting splices in a roll and allows them to pass all print bars without any loss of register or speed. This function protects the print heads from damage without affecting production.
Of course, to operate the machine, the operator must be able to master the workflow. With the Gallus One, setup assistants (wizards) guide the operator step-by-step through the upcoming tasks and support, working through the necessary steps systematically, making the steps easier to learn. Using a client-server architecture, tasks such as step & repeat can be taken over by either the operator or the prepress department. The latter relieves the operator and allowing them to concentrate more on downstream processes.
Automation also makes maintenance easier. In ongoing predictive service monitoring, sensors record the condition of the machine and transmit the data online to a cloud service set up by the parent company, Heidelberg. This is done in strict compliance with the European General Data Protection Regulation, which protects both personal and job-related data. The machine condition data is analysed, and if any irregularities become apparent the customer’s maintenance department is informed. In this way foreseeable faults can be rectified before they occur. This approach has proven its worth in the sheetfed sector over many years.
Cultural upheaval
These examples show how automation affects press technology and operations in label and packaging printing. Making full use of the automation possibilities involves embedding the presses in a workflow that links them to the factory management system. Despite extensive automation overall, the industry continues to rely on the technical expertise of its employees. Therefore qualified employees will continue to be indispensable in the future. To attract them, jobs need to be designed in an interesting way. Digital printing with the Gallus One is one example of technology being applied to accomplish this.