Maarten Hummelen, Marketingdirektor bei GSE, stellt einen Fahrplan für »klassenbesten« Verpackungsdruck mit Lean-Mentalität und automatisierter Farblogistik vor
Etiketten- und Verpackungsdrucker sehen sich mit starken Preiserhöhungen seitens der Farb- und Materiallieferanten sowie mit Lieferproblemen konfrontiert. Diese unwillkommenen Entwicklungen bedrohen zweifellos die Rentabilität – aber selbst dann können die Kosten für farbbezogene Probleme und ineffiziente interne Prozesse für das Druckunternehmen viel kostspieliger sein.
Die Druckfarbe durchläuft einen komplexen Weg durch den Druck-Workflow, und in jedem Stadium besteht eine gewisse Verschwendungsgefahr. Die Farbabstimmung ist vielleicht die komplizierteste von allen: Beim Versuch, die strengen Qualitätsvorgaben der Marke zu erfüllen, können Farbe und Bedruckstoff verschwendet werden; Verzögerungen dabei führen zu Maschinenstillständen. Man denke nur an den Verwaltungsaufwand für den Einkauf oder die Rückverfolgung von Druckfarben in der Lieferkette für Lebensmittelverpackungen.
Die Farblogistik – die Verwaltung aller mit der Farbe zusammenhängenden Prozesse – ist die Antwort auf die Frage, wie man Verschwendung vermeiden kann. Intelligent angewandt, gleicht sie höhere Preise mehr als aus. Mit der Anschaffung von Hightech-Geräten und Software allein ist es nicht getan. Es ist ein Kulturwandel erforderlich – insbesondere die Übernahme der vom japanischen Automobilhersteller Toyota entwickelten »Lean«-Geschäftsphilosophie.
Mit »Lean« zum Wettbewerbsvorteil
In den 1980er Jahren beherrschte Toyota den weltweiten Automobilmarkt. Das Unternehmen verkaufte qualitativ hochwertigere Autos mit weniger Mängeln, die mit weniger Arbeitsstunden, weniger Platz in den Fabriken, geringeren Lagerbeständen und kürzeren Lieferzeiten als die US-amerikanischen und europäischen Konkurrenzprodukte hergestellt wurden. Mithilfe von »Lean« hatte Toyota Prozesse, Praktiken und Gewohnheiten optimiert, so dass alles, was im Unternehmen geschah, auf die Wertschöpfung ausgerichtet war.
Lean ist eine Methode des kollektiven Denkens, um Verschwendung methodisch zu beseitigen und gleichzeitig die Wertschöpfung zu maximieren. »Respekt vor dem Menschen« und »kontinuierliche Verbesserung« stehen im Mittelpunkt dieser Philosophie: Die Mitarbeiter werden motiviert, ihre Arbeit jeden Tag besser zu machen, indem sie sich intensiv damit auseinandersetzen, um die Defizite zu verstehen und verbesserte Methoden zu entwickeln. In den letzten 30 Jahren hat diese Philosophie Unternehmen in praktisch allen Branchen verändert, von der Fertigung bis zu Finanzdienstleistungen – auch in der Druckindustrie!
Lean bietet einen starken Wettbewerbsvorteil, da die Veränderungen, die es mit sich bringt, sich direkt auf das wirtschaftliche Abschneiden auswirken. Eine Reduzierung der Verschwendung von z.B. EUR 100.000 kann einer Umsatzsteigerung in Millionenhöhe gleichkommen.
Schritte zur Perfektion mit »schlanker« Farblogistik
Die Überarbeitung der farbenbezogenen Prozesse ist ein guter Ausgangspunkt für die Einführung von Lean in einem Unternehmen, denn Probleme mit der Druckfarbe können hohe Kosten verursachen, und Markeninhaber werden keine ungenauen Farben tolerieren. Die einzige Lösung für den Verpackungsdrucker besteht darin, das Ideal »Null Ausschuss, Null Verschwendung, Null Verzögerung« anzustreben. Im Folgenden sind einige Schritte aufgezeigt, die ein Druckunternehmen mit diesem Ziel vor Augen unternehmen kann:
♦ Schritt 1: Den tatsächlichen Mehrwert definieren
Fragen Sie sich, wofür die Kunden Sie wirklich bezahlen. Das Etikett und die Verpackung, die sie verkaufen, sind ein Mittel zum Zweck: Umsatzsteigerung oder ein überzeugendes, starkes und konsistentes Branding am Verkaufsort zum Beispiel.
Der Trick besteht darin, die Prozesse zu betrachten und festzustellen, welche Kosten einen Mehrwert darstellen (z.B. Personal, Druckmaschinen und Ausrüstung), und die Kosten und Aufgaben, die keinen Mehrwert darstellen, so weit wie möglich zu reduzieren.
♦ Schritt 2: Verschwendung identifizieren
Es gibt acht Arten von Verschwendung, die alle gemessen werden sollten. Sie beziehen sich auf den Etiketten- und Verpackungsdruck in folgender Weise:
- Überproduktion: Es wird mehr Farbe oder Etiketten produziert, als der Kunde bezahlen will.
- Lagerbestand: Ohne wirksames Management steigen die Lagerhaltungskosten.
- Wartezeiten: Umrüstzeiten für Kleinauflagen kosten mehr!
- Transport: die Kosten für den Versand. Grundfarben in großen Gebinden sind billiger als viele kleine Aufträge.
- Bewegung: Übermäßige Laufarbeit bei der internen Handhabung und dem Transport von Farben innerhalb der Produktion.
- Überproduktion: Verwaltungskosten für den Einkauf, die Lagerung, die Überwachung, die Bereitstellung oder das Anmischen der Farben durch den Lieferanten.
- Nacharbeit / Ausschuss: Verschwendung von Material, Arbeitskräften, Ausfall- und Produktionszeit.
- Menschliches Talent: Übermäßige manuelle Eingriffe – von der Verwaltung bis zum manuellen Mischen von Druckfarben – führen dazu, dass die Mitarbeiter ihr produktives oder kreatives Potenzial weniger gut ausschöpfen können.
♦ Schritt 3: Reorganisation des Arbeitsplatzes
Die Reorganisation des Arbeitsplatzes schafft die Voraussetzungen dafür, dass Verschwendung beseitigt und Probleme an der Quelle gelöst werden können. Die Umsetzung des »Lean 5S-Programms« führt zu einem »Boxenstopp«-Szenario, bei dem das Einrichten in wenigen Minuten erfolgt. Die fünf Elemente sind:
- Sort (Sortieren) – Entfernen Sie alle Gegenstände im Druckfarbenraum, die nicht im Arbeitsbereich verwendet werden.
- Set in order (Anordnen) – alle Gegenstände so anordnen, dass sie bei Bedarf innerhalb von 30 Sekunden gefunden werden können.
- Shine (Putzen) – Werkzeuge, Geräte und Oberflächen reinigen und überprüfen, um Probleme wie Leckagen oder Beschädigungen sofort zu erkennen.
- Standardise (Standardisieren) – einen organisierten Arbeitsplatz zu einer Erwartung machen. Dies erfordert Führungsqualitäten und eine klare Kommunikation zur Vereinbarung von Best-Practice-Standards, so dass jeder seine Verantwortung kennt und weiß, wie wichtig es ist, sie zu erfüllen.
- Sustain (Aufrechterhalten) – die vier vorangegangenen Verfahren müssen zur Gewohnheit werden. Verhindern Sie »Rückschritte« durch regelmäßige Audits und suchen Sie stets nach Verbesserungen!
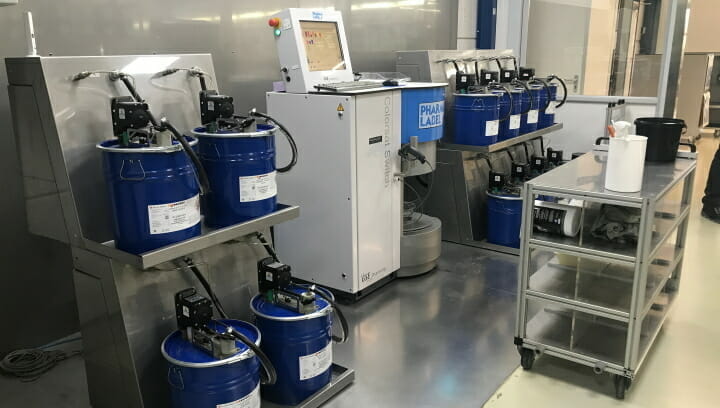
Die automatisierte Farbküche
Die Lösung zur Vermeidung von Farbabfällen und zur Erzielung von Sonderfarben auf Abruf ist ein Dosiersystem, eine spektralphotometrische Farbmessung und – für Anwender des Flexodrucks – ein Nassprüfungssystem.
Farbdosiersysteme erzeugen spezielle Farbtöne, indem sie exakte Mengen von Grundfarben nach einem bestimmten Rezept zusammenmischen. Der Bediener gibt die Zielfarbe und die Mengenanforderungen in die Schnittstelle ein; ein Computer berechnet die Dosiermengen und aktiviert den Prozess. Die Grundfarben werden in Behältern in den Dosierkübel gegeben. Eine Charge kann in wenigen Minuten hergestellt werden.
Die Software des Dosiergeräts formuliert die Rezeptur, speichert sie, um sie bei Wiederholung eines Auftrags sofort abrufen zu können, und verarbeitet die von der Druckmaschine zurückgegebenen Farben, indem sie sie methodisch in den Speicher einlagert und in neue Rezepte einrechnet. Die Rezeptursoftware verwendet digitale Farbdaten als Zielvorgaben, die in der Regel von einem Fotospektrometer erzeugt werden.
Maßgeschneiderte Dosiersysteme sind für alle Etiketten- und Verpackungsanwendungen erhältlich. Sie sind modular aufgebaut, so dass zusätzliche Basiskomponenten spezifiziert oder später hinzugefügt werden können, zum Beispiel für die Verwaltung von zwei Farbsätzen. Lösemittelfarbdosierer können mit sicheren Erdungsvorrichtungen ausgestattet werden.
Ein Tisch-Nassprüfsystem misst die Farbe einer Flexodruckfarbe bei der gleichen Tonwertzunahme, die sie in der Druckmaschine erfahren wird. Dies ermöglicht eine genaue Farbvorhersage ohne Fingerabdrücke und ohne Farbanpassungen bei Auftragswechseln auf der Zieldruckmaschine.
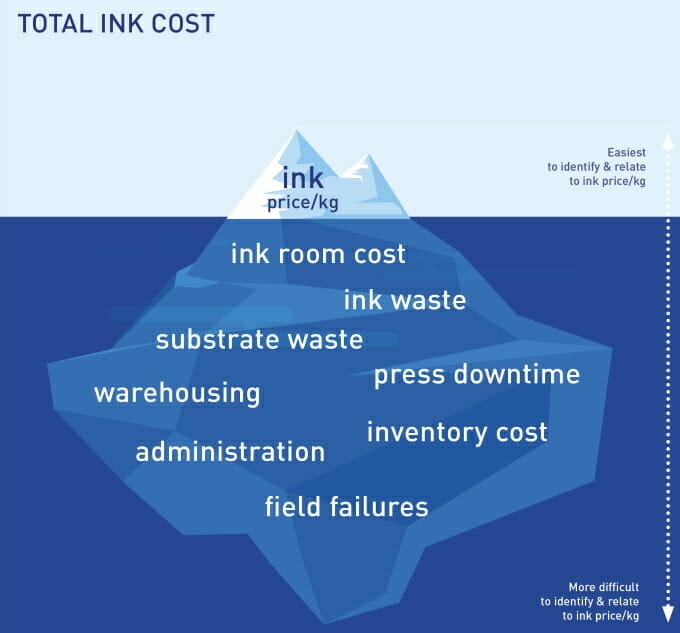
Farbkostensenkungen von bis zu 30%
Durch die Automatisierung der Farbküche können die Farbkosten um bis zu 30% gesenkt werden, und zwar dank der folgenden Vorteile:
- Die Prozesse sind schneller, es wird Zeit gespart – vor allem Betriebszeit: Ein Farbkorrektor kann einer durchschnittlichen Flexodruckerei Tausende von Euro an zusätzlicher Maschinenzeit bringen.
- Standardisierte Prozesse für Farbmessung, Dosierung und Proofing sorgen für eine vorhersehbare, wiederholbare Qualität, wobei die Farben schneller und präziser vorbereitet werden.
- Geringerer Farbverbrauch: Es wird genau so viel Farbe ausgegeben, wie benötigt wird, ohne dass ein Überschuss bestellt wird.
- Geringere Farbverschwendung: Retourfarben lassen sich leicht in neuen, computergenerierten Farbrezepten für neue Aufträge wiederverwenden.
- Organisierte Farbvorräte sind leicht auffindbar und abrufbar.
- Seltenere Bestellung von Grundfarben und Selbstmischung spart Transport-, Lager- und Verwaltungskosten.
- Geringerer Materialabfall – vor allem in der Anfangsphase.
Intelligente Farblogistik: Software integrieren
In jüngster Zeit haben Software-Fortschritte und der Einzug der Cloud Möglichkeiten zur Beschleunigung von Prozessen sowie zur Verbesserung von Kosteneinsparungen, Lagerkontrolle und Prognosen geschaffen.
Diese Fortschritte haben in der Tat eine neue Ära der »intelligenten Fertigung« ermöglicht – ein Begriff für digitale Technologien, die für transparente, integrierte und intelligente Produktionsprozesse sorgen. Beispiele für diese Technologien sind »Work-on-Screen«-Anwendungen (Ersatz von Papier durch digitale Informationen), Produktverfolgung (digitale Nachverfolgung von Produkten im Arbeitsablauf), Informationssysteme (wie Enterprise Resource Planning [ERP], Management-Informationssysteme, Druckmaschinensteuerung) und flexible Automatisierung (wie Roboter und automatische Führungsfahrzeuge).
Für die Verwaltung von Druckfarben ist eine universelle ERP-Software jedoch unzureichend. Bestehende ERP-Systeme eignen sich nur für die Nachverfolgung von Rohstoffen, die einen »linearen« Weg durch den Arbeitsablauf nehmen, ohne nach der Produktion in den Bestand zurückgeführt zu werden. Druckfarben haben nicht immer einen linearen Weg: Grundfarben werden zu Schmuckfarben gemischt, und die Wiederverwendung von Druckfarben in neuen Aufträgen ist – oder sollte – eine relativ häufige Aktivität sein, insbesondere bei Flexodruckern. Für Etiketten- und Verpackungsdrucker ist daher eine spezielle Software für die Verwaltung von Druckfarben im Workflow und die Rückmeldung von tätigkeitsbezogenen Kosteninformationen an das ERP erforderlich.
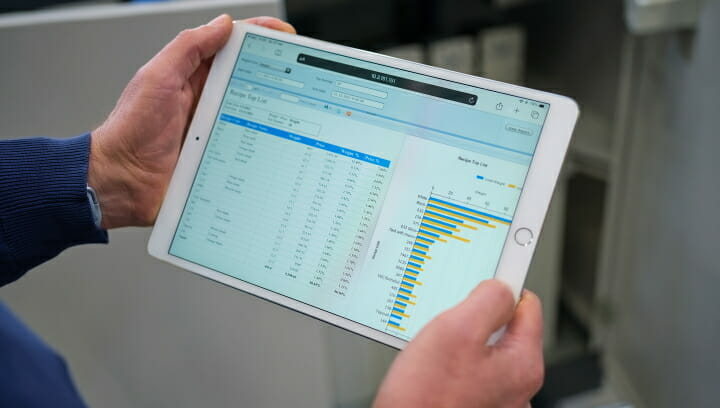
Das modulare Softwarepaket GSE Ink Manager ist eine Antwort darauf. Es bietet mehr Konnektivität, die Möglichkeit, mehr Daten zu speichern, gemeinsam zu nutzen und zu analysieren, sowie Funktionen, die eine größere Abfallreduzierung, die Rückverfolgbarkeit von Inhaltsstoffen, eine schnellere Entscheidungsfindung und strategische Planung ermöglichen. Die Benutzer können die Kombination von Paketen wählen, die ihren Bedürfnissen entspricht, unter anderem für folgende Funktionen:
- Gezielte Verwaltung von Druckfarben, einschließlich des »Clustering«“ in einer Komponente, die zur Verarbeitung mit dem Dosiergerät verbunden ist, oder Reservierung für bestimmte Aufträge.
- Integration in bestehende ERP-Software und in die Cloud.
- Durchführen von Farbkorrekturen und –anpassungen.
- Erstellung neuer Farben.
- Management-Reporting: Echtzeit-Informationen über Lagerbestand und Verbrauch; Farbkosten pro Auftrag.
- Einkauf: automatische Erstellung von Kaufempfehlungen, wenn der Bestand an Grundfarben niedrig ist.
- Rückverfolgbarkeit von Farbchargen: Verfolgung der Inhaltsstoffe über die gesamte Lieferkette, auch für wiederverwendete Rücklauffarben.
ROI-Beispiel
♦ Ein Etikettendrucker, der ursprünglich 4000 kg Druckfarbe pro Jahr verbraucht, senkt seinen Verbrauch um 20%, indem er genau die benötigte Menge ausgibt und zurückgegebene Druckfarben wiederverwendet und recycelt. Einsparungen: 20% von 4000 kg, bei einem Preis von EUR 17/kg = EUR 13.600 pro Jahr.
♦ Vor der Investition in ein Dosiergerät bestellte der Verarbeiter fertig gemischte Farben pro Druckvorgang. Ein Auftrag für 8 Druckpositionen umfasste 8 x 5 kg = 40 kg. Durch die Investition in ein Dosiergerät gibt die Druckerei nur noch eine monatliche Bestellung für den gesamten Druckbedarf auf (4000 : 12 = 334 kg), was zu 12 Bestellungen pro Jahr anstelle von 100 Bestellungen führt. Geht man davon aus, dass jede Bestellung ca. 1 Stunde Arbeit (EUR 30) erfordert. Die gesamten administrativen Einsparungen für das Unternehmen betragen (100 – 12) x EUR 30 = EUR 2640 pro Jahr.
Zusammenfassung
Um zu den Besten der Branche zu gehören, bedarf es einer Kultur der kontinuierlichen Verbesserung, der Beseitigung von Verschwendung und eines integrativen Umfelds, in dem die Mitarbeiter befähigt werden, das Beste aus sich herauszuholen. Automatisierte Technologien wie Dosierung und Proofing zur Vereinfachung und Kontrolle von Prozessen. Intelligente Softwarelösungen beschleunigen die Entscheidungsfindung und ermöglichen eine reaktionsschnelle Fertigung. Wenn diese Voraussetzungen gegeben sind, ist ein Verarbeiter auf dem Weg zum »Lieblingslieferanten«.
Und schließlich sollten Sie nicht vergessen, dass es Ihre Mitarbeiter sind, die den Wandel herbeiführen – das einzige Kapital Ihres Unternehmens, das im Laufe der Zeit an Wert gewinnt. Ein kollaboratives Umfeld, in dem sich alle Mitarbeiter in die Entscheidungsfindung einbezogen und in die Lage versetzt fühlen, einen Beitrag zu leisten, ist von entscheidender Bedeutung, um Veränderungen überhaupt erst möglich zu machen.
GSE hat einen neuen Blog, InkConnection, ins Leben gerufen, der Etiketten- und Verpackungsverarbeitern helfen soll, Wettbewerbsvorteile zu erzielen und tintenbezogene Prozesse zu verbessern. http://www.inkconnection.org/