Im Rahmen einer neuen Zusammenarbeit zwischen Esko und Bobst wurde eine bahnbrechende Innovation entwickelt, die die Zeit für die Farbabstimmung mehr als halbiert, die Ausfallzeiten um 70% reduziert und die Effizienz von Tiefdruckereien deutlich steigert.
smartGRAVURE wurde von Bobst in Zusammenarbeit mit Esko entwickelt als Lösung für die Druckvorstufe und das Inline-Farbleseelement. Das Ergebnis ist ein neues Tool, mit dem Tiefdruckereien von einem vollständig digitalisierten Workflow profitieren können, der eine außergewöhnliche und gleichbleibende Qualität produziert, den Abfall von Bedruckstoffen und Druckfarben minimiert und die Effizienz im gesamten Druckprozess maximiert.
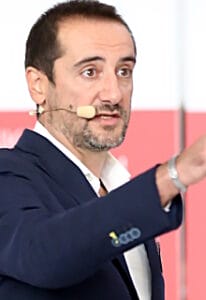
Davide Rossello, Bobst Competence Center Manager & R&D Process Manager, Gravure, sagte, dass das Projekt im Jahr 2019 begann, als Esko in der Druckvorstufe spannende Arbeiten im Bereich des Extended Color Gamut-Drucks durchführte. »Bei Bobst Italien stellen wir immer Tiefdruck her«, sagte er. »Die Farbsteuerung ist der letzte Schritt auf dieser Reise – aber während dieser Prozess in der Druckvorstufe begann, hat er sich nun an das Ende des Druckprozesses verlagert.«
Vereinfachung der Farbanpassungsprozesse
»Wir wollten etwas Neues einführen. Tiefdruck ist eine stabile Technologie mit weniger Variablen als andere und ist immer der Bezugspunkt, wenn es um den Vergleich von Druckqualitätsergebnissen geht, und unser Schwerpunkt liegt auf der Verbesserung von Produktivität, Management und Effizienz.«
Er erläuterte, dass die Fragmentierung von Aufträgen mit der unterschiedlichen Anzahl von Aufträgen und Umstellungen bedeutet, dass Tiefdrucker traditionell vor Herausforderungen stehen, wenn sie den Zylinder für jede Farbe wechseln, wobei der Farbeinstellungsprozess viel Zeit erfordert, um die höchste Qualität zu erreichen.
»Da Bobst nicht über ein Farbanpassungstool verfügte, lag es in den Händen des Kunden«, sagte er. »Wir entschieden uns, die Einrichtezeit zu betrachten und zu sagen: ›OK, lass uns die Druckmaschinen unserer Kunden vereinfachen und diesen Prozess digitalisieren‹. Wir wussten, dass wir für den ECG-Druck die optimale Technologie zur Überprüfung des Druckregisters brauchten, um die Farbanpassung zu vereinfachen. Wir brauchten eine erstklassige Farbvorstufensoftware und standen vor der Herausforderung, diese mit der Maschine zu kombinieren, um die Farbe richtig zu fixieren. Hier kommt Esko ins Spiel«.
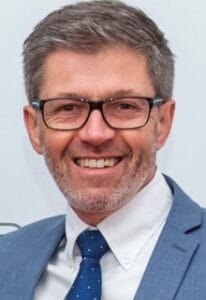
Laut David Naisby, Business Development Director bei Esko, war die Schlüsseltechnologie bei der Entwicklung einer Lösung das AVT SpectraLab-System – die marktführende Technologie, die 2012 erstmals vorgestellt wurde und deren dritte und neueste Generation SpectraLab XF ist.
»Die Weiterentwicklung dieses ISO-zertifizierten Messgeräts hat viele Jahre gedauert, und heute sind wir stolz darauf, dass wir in der Lage sind, sowohl den Medienstreifen als auch das Druckbild während der Inbetriebnahme der Druckmaschine und während des Druckprozesses zu messen. Dies ist eine Technologie, von der jeder Druckmaschinenhersteller profitieren kann. Bobst hat klar erkannt, wie sie dies in einen Vorteil für ihre Kunden verwandeln kann, um die Produktivität zu verbessern, die Umweltbelastung zu reduzieren und letztendlich den Gewinn zu steigern.«
Das Bobst-Team bewertete mehrere Technologien und kam zu dem Schluss, dass Esko die vollständige Lösung für die technologischen Anforderungen des Unternehmens bietet. »Die Forschungs- und Entwicklungsabteilungen der beiden Unternehmen haben gemeinsam eine Software entwickelt, die die Interaktion des Bedieners mit dem AVT SpectraLab XF vereinfacht und die Anzeige von Live-Dichte- und Farbinformationen auf der BOBST-Benutzeroberfläche ermöglicht. Die Tests in 2022 erbrachten sehr gute Ergebnisse. Wir sind nun in der Lage, die Messwerte der Druckmaschine mit dem X-Rite eXact Spektralphotometer abzugleichen, so dass die branchenüblichen Toleranzen innerhalb eines Delta E liegen«, so David Naisby.
»Angesichts des Trends zu kürzeren Auflagen ist die Farbabstimmung und der damit verbundene Zeit- und Makulaturaufwand ein erheblicher Engpass, der zu inakzeptablen Kosten für den Verarbeiter führt. Mit smartGRAVURE haben wir mit dieser Lösung einen großen Schritt nach vorne gemacht.«
Davide Rossello von Bobst fügte hinzu: »Esko hat uns im Wesentlichen das Rezept gegeben, wie wir die Farbe in der Maschine digital fixieren können. Mit smartGRAVURE haben wir nun 100% Kontrolle über das, was in der Druckmaschine passiert. Mit diesem neuen Tool können die Anwender alle Fehlregistrierungen, Unterschiede bei der Tonwertzunahme (TVI) und die Farbkontrolle in Einklang bringen. Delta-E-Toleranzen sind garantiert, und es ermöglicht auch die Anpassung von Prozessfarben, die wir im Falle einer Abweichung messen können, wodurch der Kreislauf der Farbabstimmung in der Druckmaschine selbst effektiv geschlossen wird.«
»Im Hinblick auf die Produktionssteuerung bedeutet dies, dass die Wiederholbarkeit gewährleistet ist, da alles digitalisiert ist. Die Maschine nimmt jetzt die Anpassungen vor, um alles in Einklang mit dem Benchmark zu bringen. Dies ist eine neue Technologie, die in eine Tiefdruckmaschine implementiert werden kann, um dem Kunden eine Produktion zu ermöglichen, die vom ersten bis zum letzten Meter vollständig kontrolliert ist.«
Beseitigung gängiger Engpässe
Da etwa 50% der Zeit für das Einrichten und 50% für die Produktion aufgewendet werden, analysierten die Entwicklungsexperten von Esko und Bobst die Daten und ermittelten, wo die Engpässe im Tiefdruckprozess lagen.
»Wir erkannten, dass der Kunde zwischen 45 und 120 Minuten für die Farbabstimmung benötigte. Das ist natürlich ein erheblicher Zeitverlust. Da wir Maschinenhersteller sind, haben wir uns nie wirklich mit der chemischen Zusammensetzung der für die Sonderfarben verwendeten Druckfarben befasst. Wir haben eine ausgezeichnete Beziehung zu Esko, und da wir einen Partner aus der Druckvorstufe brauchten, einen Experten für Software und vorzugsweise eine Lösung, die sich in die Workflow-Lösung Esko Automation Engine integrieren ließ, um sowohl die Zusammensetzung als auch die Farbe zu lesen, war es absolut sinnvoll, zusammenzuarbeiten.«
Esko war vom ersten Tag an ein wichtiger Bestandteil des Projekts – der erste Fingerabdruck wurde sogar mit einem Esko-Logo gedruckt. David Naisby von Esko erklärte: »Der Traum aller Verarbeiter ist es, eine Druckmaschine automatisch laufen lassen zu können, ohne die Farbe anpassen zu müssen. Wir sind stolz darauf, dass wir mit dieser Partnerschaft den Betreibern helfen können, ihr Ziel zu erreichen.«
»Der grundlegende Teil dieses Prozesses ist die genaue Messung der Farbe, da alles im Workflow davon abhängt. Zweitens muss der Farbdaten-Workflow vereinfacht werden. Es kann nicht sein, dass die Drucker komplexe Solldichte- und Farbwerte an der Druckmaschine eingeben. Um dies zu erreichen, ist das SpectraLab XF mit dem X-Rite ColorCert-Produkt verbunden, das sich in der Esko S2 Cloud-Lösung befindet. Spezifische Farbzielinformationen für den Auftrag werden an die Druckmaschine gesendet und das SpectraLab XF wird automatisch mit den richtigen Werten für jedes Druckwerk eingestellt.«
Das AVT SpectraLab XF von Esko misst bei hohen Produktionsgeschwindigkeiten mit hoher Frequenz und gewährleistet eine perfekte Farbabstimmung und -konsistenz gemäß der Markenspezifikation, hilft bei der Reduzierung von Makulatur, indem es auf Farbdichteabweichungen hinweist und die Bediener dabei unterstützt, die erforderlichen Farbtoleranzen wieder zu erreichen. Mit den neuen Farbkontrollfunktionen von Bobst wird diese Fähigkeit in eine automatisierte Closed-Loop-Farblösung umgesetzt.«
»Unser erster Test fand 2019 statt, und jetzt haben wir es endlich auf einer Maschine in unserem Kompetenzzentrum eingerichtet«, fügt Davide Rossello hinzu. »Was den Unterschied angeht, den smartGRAVURE macht, ist es einfach besser. Es nimmt automatische Anpassungen für die Basis und die Farbverlängerer vor, um die Farbe auf die Zieldichte zu bringen.«
»In Tests wurden mit smartGRAVURE 94,6% der erweiterten Farbskala erreicht, der niedrigste Wert lag bei beeindruckenden 89%“, sagte er. »Ein Bereich von 89–95% ist erstaunlich hoch, wobei nur einige sehr spezielle Farben fehlen.«
Farbqualität sichern, Zeit sparen, Makulatur reduzieren
»Was bis heute Stunden gedauert hat, kann jetzt auf unter 20 Minuten reduziert werden, je nach Auftrag und Farbe. Um den Zylinder auszutauschen, sind ab dem Moment, in dem die Maschine anhält, nur noch ein paar mechanische Änderungen erforderlich, und wir müssen nichts mehr waschen. Bei einem neuen Auftrag sollte keine Farbeinstellung erforderlich sein, so dass wir den Zylinder viel schneller austauschen können und in weniger als 20 Minuten wieder mit dem neuen Auftrag fertig sind«, so Davide Rossello.
Laut David Naisby sind die Zahlen in Bezug auf die tatsächlichen Einsparungen und Vorteile ebenso beeindruckend wie verblüffend. »Die gesteigerte Effizienz bedeutet, dass die Leerlaufzeit um bis zu 70% reduziert wird, wobei die Zeit, die früher etwa 90 Minuten betrug, auf weniger als eine halbe Stunde reduziert wird. Dies schafft eindeutig zusätzliche Vorteile in Bezug auf die Verfügbarkeit der Druckmaschinen und eine insgesamt verbesserte Produktivität.«
Um die Farbe zu messen, müssen die Bediener der Tiefdruckmaschinen einen Testlauf drucken, bei dem sie mehrmals starten und stoppen müssen, um die Farbanpassungsgeschwindigkeit zu erreichen, und jedes Mal etwa 300–350 Laufmeter drucken, bevor sie den Testlauf wiederholen, bis die Farbe perfekt ist. »Das ist eine Menge Druckmaterial, das verschwendet wird, sowohl in Bezug auf den Bedruckstoff und die Farbe als auch in Bezug auf den Energie- und Zeitaufwand«, so David Naisby. »Mit smartGRAVURE kann dies nun mit einem einzigen Stopp und Start erreicht werden, was eine Materialeinsparung von bis zu 60% bei der Umstellung bedeutet.
»Dies bringt nicht nur große Vorteile in Bezug auf die Materialeinsparungen, sondern verhindert auch die Verschwendung, da die Druckkunden ein Problem frühzeitig erkennen können und nicht erst, wenn die ganze Rolle fertig ist.«
In Bezug auf die Farbqualität erläuterte Davide Rossello, dass bei einem Pantone-Validierungstest die erste »Print total of colors«-Einstufung erzielt wurde, die jemals von einer Tiefdruckerei erreicht wurde. »Dies geschah in einem Durchgang auf der RS 6003 in unserem Kompetenzzentrum mit 2369 Farben, wobei wir eine Bewertung von 92,1% erreichten. Mit diesem neuen, von Bobst und Esko entwickelten Tool können Tiefdrucker einen durchgängig digitalisierten Prozess nutzen, der es ihnen ermöglicht, die höchsten Industriestandards mit Leichtigkeit zu erfüllen und zu übertreffen.« (Bildquelle: Esko / Bobst)
〉 www.bobst.com
〉 www.esko.com