Dieter Finna (Click here for a German version)
What does a label printer require for the production of low migration jobs with UV inkjet inks according to »Good Manufacturing Practice«, i.e. GMP-compliant? The answer was provided by press manufacturer Gallus during an Open Day in February of this year. A Gallus Labelfire, with comprehensive equipment for low-migration jobs as well as a new generation of UV inks from Heidelberg that has passed the practical tests with its migration-optimized properties were presented.
There are numerous factors that influence the migration behavior of printed label stock. A slight migration of substances from it can never be completely avoided. However, it must be ensured that the narrow tolerances of the migration values are not exceeded. And even if a label printer has complied with all the parameters of Good Manufacturing Practice (GMP) during the production of the label material, it is possible that the migration test of a food manufacturer may show values above the tolerable values. There can be many reasons for this, e.g. storage time or storage temperature can influence the migration behavior. In such a situation it is important for the printer to be able to prove that all process steps in label production were GMP-compliant.
Technical solution with documentation
Gallus presented a Labelfire with a newly developed two-stage drying system at the Print Media Center Label in St. Gallen/CH as a solution to such challenges facing label printers. The innovation consists of the drying unit itself along with an additional booster. Both are located in the centre of the hybrid printing system, which consists of conventional UV flexographic printing units and a digital UV inkjet printing unit (DPU) with a maximum of 8 colours. The new drying unit and booster ensure exceptional performance in the drying process. Furthermore, the relevant parameters for the curing process are consistently recorded by both units during production. Together with Prinect prepress and a new UV inkjet ink series, this makes up a complete package that significantly reduces the risk of ink components migrating from the label into packaging.
Low migration or migration-optimized?
Often »low migration« is used as a term to emphasize that it is an ink system with a particularly low migration tendency. In this article, the term »migration optimized« will be used instead to describe this situation more accurately.
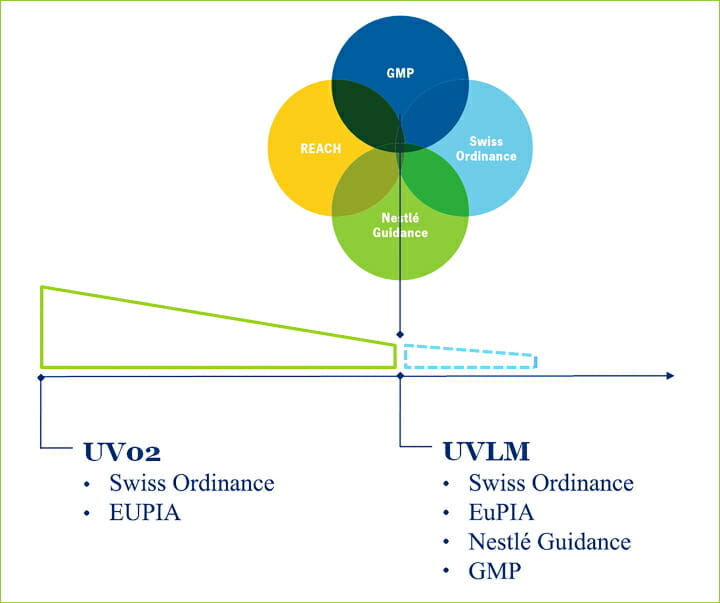
Requirements for low migration UV inkjet inks
For all Low Migration (LM) inks there is a requirement that only listed substances with a migration behaviour below the specified limits may be used in production. UV inkjet inks pose an additional challenge to the ink formulation, as the requirements for good jet capability on the one hand and lowest possible migration on the other are contradictory. An inkjet ink is described as jetting well if it transfers the individual substances in the droplets onto the substrate precisely and with the same consistency at the highest printing speed. To achieve this, the ink components must be ground so finely or be so small that they fit safely through the fine nozzles of the digital print heads. For migration-optimized inks, on the other hand, longer-chain molecules would be more suitable, as they are less mobile due to their longer structure. Print heads with a native resolution of 1200 dpi and a droplet size of 2 pl are used for fine halftone motifs in label printing, as is the case with the Gallus Labelfire 340. Such fine nozzles restrict the choice of raw materials for LM UV inkjet inks due to the described requirements.
The third generation of inks
»Heidelberg has been able to further reduce migration behavior with the formulation of the third generation of UV inks«, said Martin Leonhard, Head of Business Development at Gallus Ferd. Rüesch AG, presenting the new UV LM ink series, adding: »This was possible thanks to the selection of raw materials and the purity of the raw materials, which meet the requirements of the Swiss Ordinance, the Reach Regulation, the Nestlé Guidance and GMP specifications. The ink series itself has a very low viscosity, matched to the fineness of the nozzles. Despite a limited selection of compliant photoinitiators for this viscosity range, Heidelberger Druckmaschinen AG (Heidelberg) was able to implement this in a migration-optimized solution.«
»With the formulation of the third generation of UV inks, Heidelberg has been able to further reduce migration behaviour« explained Martin Leonhard, Head of Business Development at Gallus Ferd. Rüesch AG.
Drying under inert conditions
The performance of the new drying system of the Gallus Labelfire has been significantly improved upon when compared to the previous version. It consists of two inert curing systems, each with an output of 238 W and being water-cooled.
The special feature of this drying unit is that curing takes place in the absence of oxygen in the two inert chambers by displacing the oxygen with nitrogen. This subsequently increases the curing performance and the reactivity of the photoinitiators. »During operation, UV sensors not only permanently measure the output of the UV lamps, but the sensors also record the oxygen content in the two inert chambers. This eliminates malfunctions and production documentation can rely on a complete record of all drying parameters«, said Martin Leonhard highlighting the advantages of the new drying unit for printing migration-optimized inks.
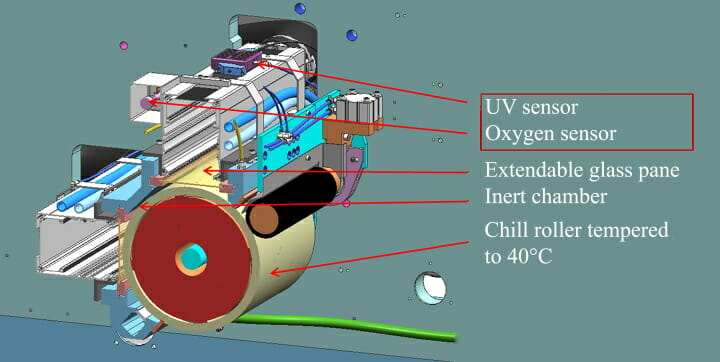
In his presentation, Leonhard also addressed the special requirements of absorbent substrates. If paper substrates or cardboard are used, it is necessary to pre-print a water-based primer that prevents UV ink from penetrating the substrate surface. He further explained: »If UV inks were able to penetrate the substrate, the ratio of monomers, oligomers and photoinitiators on the surface would change, which could lead to non-crosslinked ingredients. If the UV ink remains on the surface of the substrate, it is crosslinked by the high performance of the dryers. It should be noted that the primer used, like all raw and auxiliary materials, must also meet the requirements for migration-optimized products.«
The drying chambers are supplied with nitrogen by the adsorption principle using a carbon molecular sieve. The adsorption process separates the nitrogen molecules of the aspirated ambient air from the oxygen molecules or inert gases and ensures continuous nitrogen production at a desired purity of up to 99.99%.
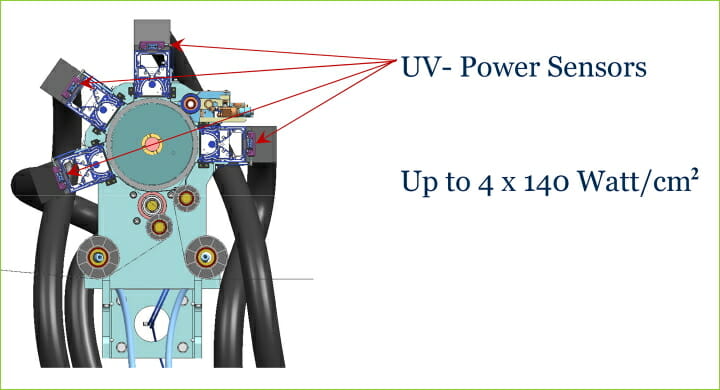
Booster for drying at higher speeds
In addition to the drying unit, a booster is available for the curing of UV inkjet inks, which boosts the drying performance for printing speeds above 35 m/min. »The booster has four lamps, each with 140 W/cm2 curing power, which ensure complete curing of the UV inkjet inks even at maximum production speed. These lamps, too, are each equipped with sensors that monitor and record the function so that this processing step is also documented and verifiable«, Leonhard demonstrated the second part of the new drying system.
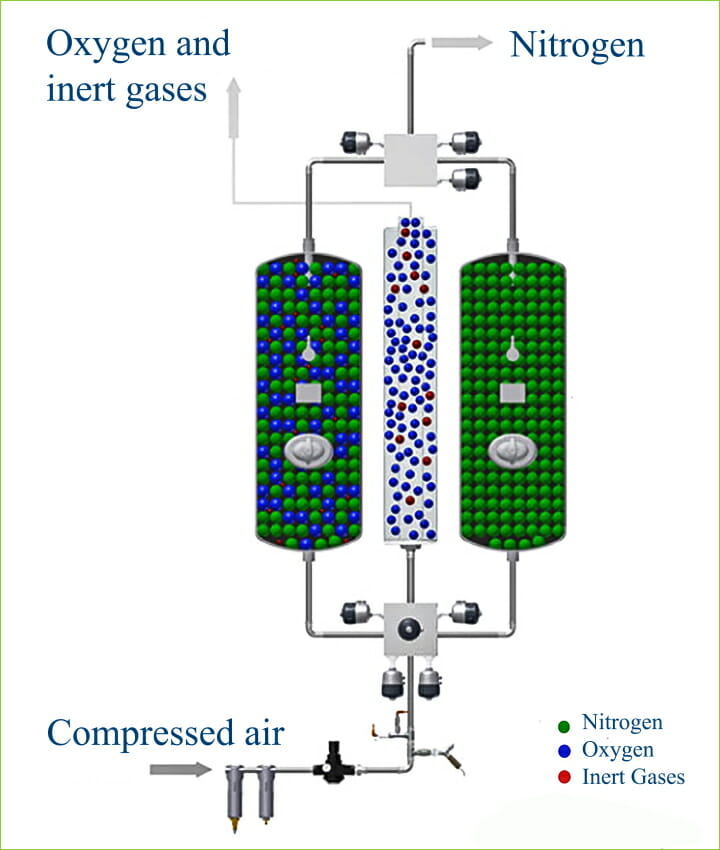
Prinect Prepress and Pressroom Manager
Support in the effort to achieve the lowest possible migration values also comes from the prepress. The Prinect production workflow enables prepress staff to intervene in the ink buildup of print jobs by reducing the ink film thickness. This prevents an unnecessarily thick ink film and reduces the migration potential. As an example, Leonhard cited the reduction of ink coverage for the same Pantone colour value from 280% (C=100%, M=100%, Y= 80%) to 220% (C=80%, M=60%, O=40%; Y= 40%) by using gamut extenders, which results in an overall reduction of approximately 21%.
Migration tests
Migration tests or model calculations are a safeguard for the manufacturer to prove that the delivered material meets the specification. Printers turn to specialized laboratories for this purpose, which carry out migration tests with defined simulants under defined testing conditions.
»During operation, UV sensors not only permanently measure the output of the UV lamps, but the sensors also record the oxygen content in the two inert chambers.« Martin Leonhard, Head of Business Development at Gallus Ferd. Rüesch AG.
During the Open Day, Christoph Losher from Fabes Forschungs-GmbH presented an apparatus that Fabes has developed for migration tests in cooperation with the company Gaßner Glastechnik. For the test itself, a printed foil is clamped in the MigraCell apparatus with the printed image facing downwards and the food simulant is filled in the upper part. After a defined time of mass transfer, the simulant is analyzed in a gas chromatograph. Here it is important for the institute to know which substances are to be searched for. For printing inks they are specified in the »Statements of Composition« of the printing ink. With the result of the GC analysis it should be noted that a statement from this only refers to the examined sample under the defined test conditions.
To enable label printers to form their own impressions of the practical suitability of the Gallus Labelfire with low-migration equipment, they can test day-to-day jobs according to their own criteria at the demo centres in St. Gallen in Switzerland and Wiesloch in Germany and consequently have the results checked by specialist laboratories.
GMP-compliant production method in practical tests
Label production according to Good Manufacturing Practice is a complex issue that places high demands on label manufacturing. By using the Gallus Labelfire in the tobacco industry, Gallus was quick to address the most demanding requirements in terms of printing technology and sensor technology for inkjet inks and developed practical solutions for both. Building on this experience, Gallus has tailored its expertise to further develop digital or hybrid printing systems in order to meet the requirements of »Good Manufacturing Practice«. The addition of an innovative drying unit plus booster to the Labelfire is a solution developed for practical applications that supports label printers in their day-to-day business with GMP-compliant production methods. This solution makes the very complex topic of »Good Manufacturing Practice« in daily practice much easier for printing companies in the label and narrow-web packaging sector to master and implement.