Helmut Mathes
ACIMGA, der Verband der italienischen Hersteller von Maschinen und Zubehör für die Druck- sowie Papier und Karton verarbeitende Industrie, hatte im Oktober 2021 in Florenz die zweite Konferenz der neu gegründeten Gruppe »Roto4All« organisiert. Die Veranstaltung zählte – trotz der Pandemie-Beschränkungen – über 100 Teilnehmer. Die erste Konferenz hatte im Frühjahr 2020 als Webinar mit über 450 Teilnehmern stattgefunden. Die 12 Sprecher behandelten mit ihren Präsentationen das gesamte Panorama, wobei nachstehend nur auf einige im Detail eingegangen wird
Die Roto4All-Gruppe hat sich aus Maschinenherstellern, Druckereien und Vorstufenbetrieben einerseits und Markeninhabern, Grafikern, Verpackungsgestaltern und Verpackungseinkäufern andererseits formiert. Alle Firmen, die in diesem Sektor tätig sind, können Mitglieder werden. Bei den Treffen entstehen Dialoge, welche den Grafikern und Markeninhabern verständlich machen, wo die Grenzen der Drucker liegen, und diese ihrerseits verstehen, was der Markt verlangt. Dies sollte in einem erhöhten und vor allem verlängerten Einsatz des Tiefdrucks in der Herstellung von Verpackungen resultieren. Auch die Neuentwicklungen in der Tiefdruckzylinderherstellung, welche diesem einfachen und ausgereiften Druckverfahren in Zukunft auch schnellere und billigere Druckformen ermöglichen, zeigen in diese Richtung.
Allerdings ist hierbei jedoch auch zu bedenken, dass in Skandinavien keine Tiefdruckmaschinen mehr in Produktion sind – mit Ausnahme einer letzten Maschine in Dänemark, auf der noch Verpackungen produziert werden. Diese Tiefdruckrotationen wurden vor allem deswegen abgebaut, weil man sah, wie schleppend sich die Neuentwicklungen im Tiefdruck etablierten. Deshalb erfolgte der Umstieg auf den dynamischen Flexodruck, der heute praktisch die gleiche Druckqualität bietet – aber bei bedeutend niedrigen Kosten. Es sind neben Asien vor allem Deutschland, Benelux, Frankreich und Italien die in den Tiefdruck investieren, wobei vor allem in Europa die sprachbedingten Auflagenhöhen eine Rolle spielen. Italien nimmt dabei eine Sonderstellung ein, da es eine Führungsposition im Bau von Tief- und Flexodruckmaschinen einnimmt – und seit rund 30 Jahren keine Tiefdruckmaschinen mehr importiert. In Italien produzieren über 120 Tiefdrucklinien Verpackungen. In 2020 hatte Italien Druckmaschinen im Wert von EUR 436,2 Mio. exportiert – davon entfielen EUR 142,2 Mio. auf Flexodruckmaschinen und EUR 294 Mio. auf Tiefdruckmaschinen und Teile davon.
Gravure Aimcal Alliance
Die Acimga hatte auch die GAA (Gravure Aimcal Alliance) – zur Teilnahme nach Florenz eingeladen. Die Allianz verfolgt in den USA schon länger als Roto4All das gleiche Ziel, Tiefdruck zu fördern.
Die GAA promotet den Tiefdruck, unterstützt Personalschulung, präsentiert technische Neuheiten, unterstützt die »grüne« Entwicklung sowie Verbesserung von Farben, Bedruckstoffen, Druckmaschinen, Trocknern, Zylinderherstellung, usw. Aktuelle Projekte sind z.B. die erweiterte Haftung für Recyling oder Entsorgung der Verpackungen; Neue Druckfarben, die von Folien entfernbar sind; Ersatz der Kunststoff-Folien mit Papierlaminaten.
Flexible Verpackung in 2020 – Gesamtumsatz: USD 97,2 Mrd.
– Nordamerika USD 27,2 Mrd.
– Mittel-/Südamerika USD 4,9 Mrd.
– Zentral-/Ost-Asien USD 26,2 Mrd.
– Südost-Asien/Ozeanien USD 15,5 Mrd.
– Mittlerer Osten/Afrika USD 4,9 Mrd.
– West-Europa USD 14,6 Mrd.
– Ost-Europa USD 3,9 Mrd.
Flexible Verpackung im US-Markt, aufgeteilt nach Marktsegmenten
Gesamtvolumen USD 34,8 Mrd
– Lebensmittel USD 20,3 Mrd.
– Getränkeverpackung USD 1,9 Mrd.
– Körperpflege USD 1,7 Mrd.
– Tierfutter USD 1,0 Mrd.
– Tabakwaren USD 0,18 Mrd.
– Non-Food/Allgemeine Verpackung USD 1,7 Mrd.
– Non-Food/Gesetzliche Verpackungen USD 0,2 Mrd.
– Industrieverpackungen USD 2,2 Mrd.
– Medizin/Pharma-Verpackung USD 4,9 Mrd.
– Allgemeine Verbraucherverpackungen USD 0,6 Mrd.
Bedruckte Folien waschen
Die niederländische Polymont BV in Nijkerk/NL, Mitglied der GAA, ist Hersteller von Reinigungsanalagen für Flexodruckplatten und Tiefdruckzylinder. Dazu gehört auch der Polymount Film Cleaner –ein Waschanlage die bedruckte Folien von Farbe reinigt. Derzeit sind weltweit rund 10 Anlagen installiert. Die Maschine wäscht Folien (Bahnbreiten bis 1300 bzw. 1650 mm, max. Rollendurchmesser 800 mm), die mit lösemittel- oder wasserbasierten Farben im Tief- oder Flexodruck bedruckt sind, bei 100–150 m/min Bahngeschwindigkeit. Die bedruckte Folie durchläuft zwei Wasch- und Spülbäder mit Bürsten und Gummirakelreinigung und verlässt getrocknet die 5,90 m lange Anlage. Größere Rollendurchmesser erfordern Standard-Auf- und Abwickler mit Bahnein- und -auszugsgruppe.
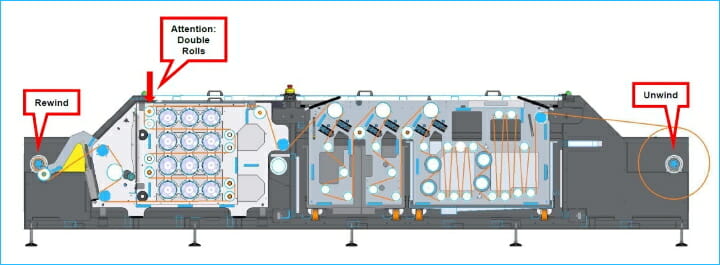
Eventuelle Farbrestemigration wird durch das abschließende Wasserbad eliminiert. Die gereinigten Filme können für neue Jobs eingesetzt werden. Die Farben werden in dem speziellen lösemittelfreien Waschmittel aufgelöst, das keinen Ex-Schutz erfordert; die Farbreste werden als Schlamm ausgeworfen. Gewaschen werden alle Folien die im Tief- und Flexodruck eingesetzt werden, mit der Ausnahme von PVC- und LDPE-Folien dünner als 30 µm.
ICR SpA
Das Unternehmen ICR SpA Incisione Cilindri Rotocalco, Origgio, VA/I, gilt als Gründer der Tiefdruckgruppe Roto4All innerhalb der Acimga in 2019. Präsident der Tiefdruckgruppe ist Gianmatteo Maggioni, Geschäftsführer der ICR SpA, dem führenden Graveur von Tiefdruckzylindern in Italien. Mit 67 Mitarbeitern wird ein Umsatz von EUR 6,5 Mio. erzielt. Pro Jahr werden rund 16.000 Zylinder graviert – 13.000 mit elektromechanischer Gravur, 3000 mit autotypischer Gravur mit Laserbelichtung, Ballenbreiten bis 3650 mm, Abschnittlängen 200–1400 mm. Dazu kommen 950 Stahlzylinder und 3000 Farbauszüge für Druckereien.
ICR arbeitet mit fünf Graviermaschinen mit 8 Gravurköpfen und vier K 500 G3 Twin Anlagen mit 8 Gravurköpfen (alle von Hell Gravure Systems). Dazu kommen die beiden automatischen elektrolytischen Gravurbadlinien »Exactus« mit Zylinderbeschichtung und Laserbelichtung: Diese Thermalgravur Technologielinien wurden von Mario Maggioni entworfen und von Acigraf Graphic Equipments, Ornago, MB/I gebaut. Der erste druckbereite Zylinder wird nach 40 Minuten ausgelegt und dann alle 10 Minuten der Nächste. Dazu kommt eine Autocon von K.Walter, 3D Scanner, drei Heaford Andruckmaschinen mit einer Farbmischstation, die direkt mit der Reproabteilung verbunden ist. Hinzu kommen galvanische Bäder und Zylinderpoliermaschinen.
Tiefdruck ist eine ausgereifte Drucktechnologie, die seit etwa 30 Jahren vom Flexodruck und seit etwa 10 Jahren auch vom Digitaldruck »angegriffen« wird. Das Verfahren hat grosse Auftragsvolumina an den Flexodruck verloren, weil dessen Kosten vor allem bei kleineren Auflagen niedriger ist – bei seit Jahren ebenbürtiger Druckqualität. Da der Tiefdruck ein sehr einfaches Druckverfahren ist, dessen Druckqualität weitgehend von der Zylindergravur bestimmt wird, versucht man mit neuen Technologien, die Zylinderherstellung zu beschleunigen und vor allem kostengünstiger zu machen. Neue Umweltschutzgesetze setzen dabei den Tiefdruck einem großen Zeitdruck aus.
Die ICR SpA arbeitet eng zusammen mit dem Istituto Italiano Imballagio (Italian Institute of Packaging), mit ITSAR (Istituto Tecnico Superiore Angelo Rizzoli – Technisches Institut Angelo Rizzoli), der ISO und der UNI (zwei Vereinigungen die sich um Normierung und Standardisierung in der Verpackungsherstellung kümmern). Dazu kommen die GAA (Sitz in den USA), die ERA (Sitz in Deutschland) und die italienischen Fachverbände GIFLEX (Verband der flexiblen Verpackungdrucker) und GIFCO (Verband der Wellpappenhersteller).
GIFLEX
Im Verband der italienischen Drucker flexibler Verpackungen sind 40 Betriebe mit rund 10.000 Beschäftigten organisiert. Sie produzieren auf 120 Tiefdruckrotationen, 60 Flexodruckmaschinen, 110 Laminieranlagen und 8 Linien für Extrusionsbeschichtung etwa 80% der in Italien hergestellten flexiblen Verpackungen. Die Gesamtproduktion flexibler Verpackungen liegt bei rund 400.000 to jährlich, wovon 13% auf Flüssigkeits-Verpackungen entfallen. Der Gesamtumsatz für flexible Verpackungen belief sich in 2020 in Europa auf über EUR 15 Mrd. wovon über EUR 3 Mrd. auf Italien entfielen – mehr als 50% gingen in den Export.
Giflex rechnet mit einer starken Reduzierung der Abfallmengen die bei der Verpackungserstellung in Europa entstehen und sich derzeit jährlich auf rund 47,6 Mio. to belaufen – 18,8 Mio. to für steife Primärverpackungen (Getränkeverpackungen, Glas, Metall, Kunststoff), 25,3 Mio. to bei Kartonverpackungen und 3,7 Mio. to bei flexiblen Verpackungen. Gemäß der Giflex könnte die Abfallmenge von 47,7 Mio. to auf etwa 26,6 Mio. to reduziert werden, wenn Faltschachteln weitgehend durch flexible Verpackungen ersetzt würden – also Folienlaminate oder Papier mit Folie oder Metallfolien sowie zusätzlichen Beschichtungen (Standbeutelprinzip für Portionsverpackungen und mit Wiederverschluss für größere und Familienverpackungen). Es verblieben damit nur die üblichen Wellpappe-Transportverpackungen und die Waren gehen vom Regal in die Einkaufstaschen. Daraus würde sich als Nebeneffekt bei den steifen Verpackungen eine Zunahme der Liquidverpackungen (eigentlich Faltschachteln) ergeben, vor allem im Getränkebereich. Die erwähnten 18,8 Mio. to könnten so auf 4 Mio. to sinken.
Bei den Sekundärverpackungen aus Wellpappe wird sich wenig verändern, weil es reine Transportverpackungen sind: Im Bereich der Mikrowelle ist eine starke Zunahme zu erwarten, da sie den flachliegenden Vollkarton ersetzen wird. All dies geht allerdings gegen die Tendenz weg vom Kunststoff und hin zu Karton/Papier als Verpackungsmaterial – der Materialkreislauf von der gebrauchten Verpackung zum Material für die Neuverpackung scheint mit Folien einfacher zu sein, als das Separieren von aufkaschierten Folien und Beschichtungen.
Allerdings ist zu beachten, dass Faltschachtelverpackungen fast ausschließlich im Bogenoffset hergestellt werden; Wellpappe aber weitgehend im Flexodruck bedruckt wird. Die Verbände GIFASP (Faltschachteln) und GIFCO (Wellpappe) sehen die Entwicklung etwas kritischer, weil dies die Entwicklung neuer Verpackungen und die Installation neuer Maschinen bedinge. Noch gibt es keine klare Antworten – weder in Europa, noch weltweit – wie man das Abfallvolumen reduzieren werde. Neue Verpackungsmaterialien, neue Verpackungsdesigns, Recycling und Kreislauf der Verpackungsmaterialien? Es braucht die überzeugte Mitarbeit aller, um das Verpackungsproblem zu lösen, wobei allerdings die Interessenlage sehr breit gestreut ist. Über einen Punkt gibt es keinen Zweifel: Die Verpackung ist wichtiger als der Inhalt.
Neue Fachgruppe »Flexible Verpackung«
Die Giflex hat am 16. Dezember 2021 mit der UCIMA (Vereinigung der Hersteller automatischer Verpackungsmaschinen) und der Unione Italiana Food (Lebensmittelhersteller) die neue Fachgruppe »Imballo Flessible« gegründet. Diese ist auch im Rahmen der Acimga-Fachgruppen organisiert, und soll dem Verbraucher eine komplette, einfach verfolgbare Herstellungskette der Verpackung und des Verpackungsmaterials anbieten.
Italien exportiert Verpackungsanlagen für rund EUR 11 Mrd. Die prinzipielle Aufgabe der »Imballo flessibile« besteht darin, den Kunststoff-Verpackungsabfall von jährlich 50.000 to definitiv zu reduzieren und in sich geschlossene Wiederverwendungsketten zu erstellen. Das jährliche Gesamtvolumen an Verpackungsmaterial summiert sich in Italien auf 180.000 to – 80% entfällt auf die Lebensmittelindustrie, wo vor allem Kunststoffverpackungen eingesetzt werden, die heute nur bedingt recycelbar sind (Kunststoff-Kombinationen). Die Regierungsvorgaben lauten: bis 2025 sollen 50% weniger Verpackungsmaterial eingesetzt werden und die heutigen 50.000 to Kunststoffverpackungen sollen in reduzierter Anzahl durch recycelbare, kompostierbare oder wiederverwendbare neue Materialien (Papier?) ersetzt werden. Die Kosten der Lebensmittelverpackungen entsprechen im allgemeinen etwa 10% des Wareninhaltwertes – wobei der Wareninhalt, verdorbene Lebensmittel, die Umwelt bis zu 4 mal mehr belasten.
Eine der Hauptaufgaben der neuen Fachgruppe ist eine bessere Organisation der Müllsammlung, der Wiederverwendung und die Automatisierung der Mülltrennung – Kunststoff soll nicht auf der Müllhalde oder im Verbrennungsofen landen, sondern wiederverwendet werden.
Die Gesamtkosten der Herstellung des Verpackungsmaterials, die Herstellung der Verpackung und der Transport dürfte sich in Italien auf EUR 50 Mrd. jährlich belaufen. Die flexible Verpackung wiegt nur 10% der Karton- und Papierverpackungen – das bedeutet rund 80% weniger Verpackungsmaterial, 42 Mio. to weniger CO2 bei der Herstellung, 20 Mio. m3 Wassereinsparung. Das Motto des neuen Fachverbandes, der vor allem aus Maschinenherstellern besteht, lautet »Die flexible Verpackung ist die Zukunft, und deshalb müssen wir sofort mit dem Einsatz beginnen« – was durchaus logisch klingt.
CONAI
ist ein privater italienischer Non-Profit-Verband (gegründet 1980) mit 8000 Mitgliedsfirmen, die Hersteller oder Verbraucher von Verpackungen sind. Conai kontrolliert die verschiedenen Stationen des Lebenslaufes einer Verpackung – Entwurf der Verpackung, Herstellung, Verteilung, Einsatz und Verwendung, Sammlung verbrauchter Verpackungen, Wiederaufbereitung des recycelten Materials sowie die Kontrolle der Verpackungsmaterial-Kompositionen, Kontrolle vom Rohmaterial über den Drucker bis zum Endverbraucher bzw. den Neueinsatz des recycelten Materials für neue Verpackungen.
In 2020 wurden 13,1 Mio. to Verpackungsmaterial in Umlauf gebracht – 4,6% weniger als in 2019. In 2020 wurden 10,963 Mio. to Verpackungsmaterial recycelt (2019: 9 Mio. to).
Neue Tiefdruckzylinder-Technologien
Die Maschinenfabrik Kaspar Walter GmbH & Co. KG, Marktführer im Anlagenbau der Tiefdruckzylindergravur, hat die Verlängerung des Einsatzes von Chromtrioxid [Chrom(VI)] zur Zylinderverchromung beantragt (Autorisierungsantrag ChromeXtend). Stand heute ist der Einsatz bis zum 24. September 2024 genehmigt. Ob Brüssel die Verlängerung bis 2032 (12 Jahre »Review Period« – gültig ab Antragseinreichung, d.h. bis 2032) genehmigt, ist noch unbekannt. In Europa sind 117 Standorte mit Anlagen von K.Walter davon betroffen. Das Unternehmen arbeitet an zwei Alternativen die, im Falle eines Verbotes von Chrom(VI) nach dem 24. September 2024, eine Weiterarbeit ermöglichen sollen.
Das Endziel ist das HelioChrome NEO System, das mit verchromten Zylinder die heutige Produktionsmethode weiterführt. Zur Verchromung wird im galvanischen Prozess Chrom(III) eingesetzt, das mit keinen gesundheitlichen Risiken verbunden ist, weniger Strom verbraucht und keinerlei Genehmigungen erfordert. Mit den neuen Bädern wird in 25 Minuten eine Chromschichtstärke von 25 µm Dicke erzielt. Der Energiebedarf der Bäder des HelioChrome NEO beträgt 20 A/dm2 bei 40 °C mit Chrom(III), das in der Toxität unter denen der Kupferbädern liegt; allerdings werden neue oder modifizierte Badanlagen erforderlich. Der Tiefdruck arbeitet heute mit Schichtstärken von 6–8 µm. Die erste Anlage des Slimline HelioChrome NEO arbeitet bereits bei Huhtamaki in der AutoCON Linie im Feldtest. Das neue System benützt eine neue Software zur Einstellung der Produktionsparameter und zur Kontrolle und Analyse des Gravurprozesses, der Schichtstärke und Näpfchentiefe und Konfiguration. Es ist ein vollautomatisches System das eventuell eine tägliche Wartung erfordert.
Die Alternative zu HelioChrome NEO wäre das Helio Pearl-System das mit einer Hybrid Polymerbeschichtung der Zylinder arbeitet, die mit einem Laser graviert werden. Die ersten Versuche begannen 2016; es wurden Tests mit über 400 Zylindern gemacht, bei Druckgeschwindigkeiten von 400 m/min, und gute Druckqualität erzielt. Auch dieses System befindet sich bereits im Feldtest mit Produktionläufen.
Die Herstellung eines druckbereiten Zylinders erfolgt in 90 Minuten. Die drei Schritte Oberflächenbeschichtung, das nachfolgende Oberflächenabschleifen sowie die abschließende Lasergravur dauern jeweils 30 Minuten. Auch mit diesem System nutzt man die vorhandenen Zylinder und Druckmaschinen. Der Materialabfall wird reduziert und die Investitionskosten in die Anlagen sind geringer. Alle Stahl-, Aluminium- oder Kupferzylinder sind einsetzbar. Es bestehen keine Lizenzen oder Probleme mit Abluft oder Wasserverschmutzung; der Stromverbrauch reduziert sich um etwa 80%. Das System besteht heute aus 3 Stationen: Beschichten, Abschleifen und Polieren, Gravieren (per Laser). In Zukunft wird daraus eine Linie wird mit automatischem Zylindertransport, da die Zeiten der drei Arbeitsphasen bei jedem Auftrag praktisch identisch sind. Das Helio Pearl-System befindet sich mit je einer Installation im Feldtest bei Windmöller & Hölscher und der HdM Hochschule der Medien in Stuttgart, wobei Testauflagen mit 10.000 Laufmeter mit verschiedenen Druckfarben und Druckträgern keinerlei Probleme oder Abnützungen zeigten.
Es ist noch offen welches Verfahren – Helio Pearl oder HelioChrome NEO – als Erstes ausgeliefert werden wirde. Das System Helio Pearl kann auch Tiefdruckzylinder mit der neuen Beschichtung Dynasurf von Contitech gravieren. Dynasurf ist eine Elastomer-Beschichtung herkömmlicher Zylinder, wobei die Gravur mit Laserstrahl oder der herkömmlichen elektromechanischem Stichel erfolgt. Contitech beschichtet nur die Rohzylinder.
Die Polymerbeschichtungen zeigten bisher sehr gute Druckergebnisse; das wurde auch beim System von Rossini festgestellt. Die ursprünglichen Befürchtungen der Abnützung der Zylinder durch die Rakelmesser haben sich nicht eingestellt. Wenn drei Hersteller Tiefdruckzylinder mit Polymerbeschichtung anbieten, dürfte die Zukunftsentscheidung wohl in diese Richtung gehen.
Die italienische Variante
Der bekannte Druckwalzenhersteller Rossini SpA aus Italien produziert mit 500 Personen in 8 Werken (5 in Europa, je 1 in USA, Indien und Brasilien). Vor etwa drei Jahren wurde als Neuentwicklung das Ecograv-System vorgestellt: es ähnelt dem Helio Pearl-System. Das System nutzt Stahlzylinder oder Walzen, die mit einer 2 mm dicken Polymerschicht auf Polyurethanbasis (ersetzt die klassische Chrom- und Kupferschicht) überzogen, durch UV-Licht gehärtet und danach auf den exakten Durchmesser (Drucklänge) mit einer niedrigen Oberflächenrauhheit abgeschliffen werden. Die Zylinder werden anschliessend mit den herkömmlichen Stichelgravurmaschinen elektromechanisch graviert. Rossini hat schon mehrere Testläufe mit über 1 Mio. Laufmeter bei Druckgeschwindigkeiten von 200–250 m/min gefahren. Ergebnisse: Gravierter 5%-Lichtpunkt bei Druckbeginn 20 µm Näpfchendurchmesser, nach 1 Mio. Drucke nur wenige µm Zunahme. 50%-Mittelton bei Druckbeginn Näpfchendurchmesser 117 µm, nach 1 Mio. Drucke praktisch praktisch unverändert. Bei den Tests wurden immer die üblichen Stahlrakelmesser eingesetzt.
Die Zylindergravur des Ecograv-Systems in Polymer ist nur bedingt mit der Gravur in Kupfer zu vergleichen. Abnützung durch die Rakel, die Näpfchenkonfiguration und Farbübertragung sind etwas anders. Polymer ist kein Metall, wenn auch das Druckergebnis das gleiche ist. Metall garantiert bei der Gravur 100% Wiederholbarheit.
Das Problem der Polymerbeschichtung ist die Rakel mit einer Härte bis 700 Vickers und den heutigen Chromschichten mit 1000–1200 Vickers. Die Tiefdruckzylinderoberfläche hat eine spezifische Rauhheit, die den Aufbau eines Gleitfilms gestattet und damit Beschädigungen durch der Rakel exkludiert. Heute werden 90% der Tiefdruckzylinder mit dem Stichel graviert – dieser wird in Zukunft ziemlich sicher durch den Laser ersetzt. Der Vorteil der Polymerbeschichtung ist, dass sich praktisch keine elektrostatische Energie aufbaut, und auch der Einsatz von ESA-Systemen zur besseren Farbübertragung, dem Entleeren der Farbnäpfchen, hinfällig wird.
Fingerprinttests, mit Wiederholungen, von Zylinder nach 300.000 Laufmetern, bei Druckgeschwindigkeiten von 300–350 m/min, Druck auf 12 µm PET und 20 µm BOPP-Folien mit reinen Ethylacetat-Farben sowie mit Ethylacetat- und Alkohol-basierten Farben. Druckzylinderdaten: 600 mm Druckbreite, 594 mm Rapportlänge. Zylinder im gleichen Format, aber für 7 Farbenjob auf PE/AL-Laminat, zeigten das gleiche Ergebnis. Der gleiche Job, aber mit Druckbreite 1270 mm und auf einer Breitbahnmaschine gedruckt, zeigte das gleiche Ergebnis.
Die Drucktests bei Rossini gehen weiter, vor allem um die Gravurkurven bei Wiederholaufträgen, Ersatzzylinder, verschiedene Farbsorten, verschiedene Druckgeschwindigkeiten und Druckträger zu untersuchen. Rossini arbeitet eng mit der ICR SpA zusammen. Zwei Pilotanlagen, voll digitalisiert und vollautomatisiert für die Zylinderbeschichtung, werden installiert – eine bei einer Druckerei und eine bei Rossini für Testversuche der Kunden. Das bedeutet: auch Rossini wird für eine Lieferung in 2024 bereit sein.